Multiphase Flow
Multiphase flow is present in nature and various industrial applications, such as in the nuclear industry, chemical processes, oil production, and transportation, among others. In this scenario, the Multiphase Flow Center – NUEM has developed several basic and applied researches, financed by development agencies and industries, on the detailed characterization of multiphase flow in pipes and equipment (centrifugal pumps, separators, among others).
Principal Investigator
Prof. Rigoberto E. M. Morales, Dr. (rmorales@utfpr.edu.br)
Research Topics
- Multiphase Flow in Pipes
- Multiphase Flow in Equipment
- Multiphase Flow Separatation Technology
- Computational Fluid Dynamics
Multiphase Flow In Pipes
Multiphase flows in pipes are present in different industrial activities. Since 2006, NUEM group has developed mathematical models for multiphase flows. The mathematical models comprises from simple steady-state models to more complex models for transient regimes. Three classes of models stand out: unit cell models, slug capturing model and slug tracking model. These models validation require closure relationships, empirical correlations and statistical distributions of characteristic flow parameters obtained experimentally.
NUEM group has been developing several experimental studies of multiphase flows in pipes with different configurations, carrying out experiments on horizontal, vertical, inclined pipes and with slight changes in direction. With the proper instrumentation in the experiments, characteristic flow parameters are extracted, which provide important information for understanding the phenomena involved in each scenario, in addition to providing data for input and validation of numerical models under development.
NUEM group has expertise in the development of mathematical models and experimental analysis for two-phase and three-phase flows in horizontal, vertical and changing direction pipes. In addition, variations in pipe diameter and fluid viscosity and density can be taken into account.
Multiphase Flow in Equipment
Pipes and ducts are the standard for fluid transportation in a wide range of applications. Because of this, lots of experimental data, correlations, flow maps, and models are obtained and calibrated for them. Interest in multiphase flows goes far beyond pipes though, as several other devices play an important role in many industrial processes, such as in heat transfer, multiphase separation, and pumping.
For more than a decade, the NUEM group develops theoretical, numerical, and experimental studies to investigate single and multiphase flows in a variety of equipment employed in those processes. These include corrugated ducts, hydrocyclones, gravitational separators, distribution systems, and centrifugal pumps.
With the help of NUEM’s large Multlab infrastructure and CFD capability, studies in these equipment have been providing data to our partners so they can understand how multiphase flows behave in complex geometries. The group has also developed mechanistic models to design new geometric concepts, correlations and data charts to help in process control, and other valuable information, for both academy and industry.
Multiphase Flow Separatation Technology
The separation of the different phases extracted from the oil production wells is an essential process that has been studied at NUEM. Different methods for phase separation are addressed in the group, such as hydrocyclones, flow distribution systems, gravitational separators, and floats.
With the numerical and experimental capacity present in NUEM, important results have been extracted for understanding the dynamics of multiphase flows in different types of separators, for creating mathematical models, for dimensioning equipment, and even for the development of new geometries that seek to optimize the separation process.
Computational Fluid Dynamics
Computational Fluid Dynamics, or simply CFD as it is commonly known, is a very valuable tool in fluid mechanics. Numerical flow simulations provide great flexibility to test a number of scenarios that are sometimes expensive or even impractical to accomplish with experimental methods, allowing assessment of complex flow details. Since powerful computers are becoming increasingly accessible, CFD has established itself as a definite force in fluid analysis, from fundamental academic research to applied engineering.
Working in multiple projects in this field since 2006, the NUEM group accumulates extensive experience in CFD of multiphase flows. Today, almost all NUEM research has the support of CFD as a primary or secondary tool in flow analysis, with utilization spanning through a wide range of areas, from fundamental analysis of the dynamics of rising bubbles to the performance evaluation of multistage pumps operating with multiphase flows.
Projects
Coordinator: Prof. Rigoberto E. M. Morales, Dr.
The complex nature of mixtures of fluids such as gas and liquid or two immiscible liquids poses a considerable challenge in understanding their behavior in pipes. This poses a considerable problem for industries such as energy, chemical, food and beverages, and oil and gas production since these complex flows are fundamental to their operation. Designs and developments underpinned by the models validated with accurate measurements can provide significant cost savings, increase safety, and decrease the impact of these industries on the carbon footprint. As Brazil is a rising economy, industries such as food, chemicals and oil and gas production spread rapidly across the country, these benefits would have a considerable impact on quality of life and society in general. The main source of the problems with multiphase flow is the difficulty of measuring the flows and getting the information on the distribution of the phases at any cross section of the pipe. This lack of real time data leads to poor predictive models making design tasks difficult and erroneous. This deficit in information demands the development of new class of measurement and analysis techniques that applies to two or more co-flowing fluids. UTFPR has been developing new sensors and Nottingham has been leading in multiphase phase flow measurements in pilot scale flow loops. The proposed work would see the development and calibration of a novel three phase flow measurement device. Furthermore, analysis of data interpreting the nature of the three phase flow will be carried out to develop predictive models
Partners
Coordinator: Prof. Rigoberto E. M. Morales, Dr.
In a primary processing plant, equipment is used to separate the phases that meet the required requirements, whether these are discarded or commercial. Due to space and cost limitations, efforts are being concentrated to optimize the design / dimensioning of separation systems. In this context, the present project intends to reevaluate the concept of the gravitational separator with cleaning systems and coupled flotation systems to reduce the cost and dimension, without compromising on the separation efficiency. The project will be developed numerically and experimentally. A laboratory bench on a small-scale laboratory will be built to understand the flow dynamics in the gravitational separator and the float. To understand the flow details, numerical simulations will be performed using the Computational Fluid Dynamics (DFC) technique. From the numerical and experimental results, the separation efficiency, details of the velocity fields, and phase concentrations along the flow will be evaluated. The detailed analysis of the results obtained during the development of the project will be presented via technical reports.
Financial Support
CENPES / PETROBRAS
Coordinator: Prof. Rigoberto E. M. Morales, Dr.
Project period: 2017 – current
This project aims at the experimental characterization of two-phase gas-liquid flow in horizontal and vertical pipelines at high pressures, similar to those found in oil production in deep waters (Pre-Salt), using model fluids. To achieve the proposed objective, high molecular weight gases (for example, SF6 – sulfur hexafluoride or some refrigerant fluid) and model oil of different viscosities will be used.
Financial Support
CENPES / PETROBRAS
Coordinator: Prof. Rigoberto E. M. Morales, Dr.
The fundamental objective of this proposal is to develop a numerical and experimental study of the two-phase liquid-gas flow in the presence of a flow distributor. Focused on the development of a mechanism or methodology that allows an equitable distribution of the flow. In the present stage of the studies, the flow for different water and air flow conditions, atmospheric pressure, and flow distribution in four (04) branches will be evaluated. The activities to be developed in the present project will be carried out aiming to achieve the following results: i) Definition of a configuration for the distribution of two-phase flow of liquid-gas in four (04) lines in parallel; ii) Behavior of flow patterns in the flow distribution process; iii) Proposal of an algorithm for the dimensioning of the liquid-gas two-phase flow distributor.
Financial Support
CENPES / PETROBRAS
Coordinator: Prof. Rigoberto Eleazar Melgarejo Morales, Dr.
This project aims at the numerical study of single-phase and two-phase gas-liquid flow in Submerged Centrifugal Pumps. In order to achieve the objectives, the following activities are planned: (i) Simulation of viscous flows in Submerged Centrifugal Pumps, in order to verify the corrections of the similarity laws; (ii) Numerical simulations of biphasic liquid-gas flow in Submerged Centrifugal Pumps and (iii) Experimental study of two-phase gas-liquid flow in centrifugal pumps.
Financial Support
CENPES / PETROBRAS
Coordinator: Prof. Rigoberto E. M. Morales, Dr.
Feasibility study and development of optical instrumentation for monitoring of CO2 diluted in oil and implementation of optical instrumentation for monitoring two-phase gas-liquid flow in the laboratory.
Financial Support
CENPES / PETROBRAS
Coordinator: Prof. Rigoberto E. M. Morales, Dr.
Development of advanced instrumentation combined with new signal processing techniques for extracting two-phase flows parameters and conducting flow tests involving oil and CO2.
Financial Support
CENPES / PETROBRAS
Highlighted Publications
Grigoleto, M. M., Bassani, C. L., Conte, M. G., Cozin, C., Barbuto, F. A., & Morales, R. E. M. (2021). Heat transfer modeling of non-boiling gas-liquid slug flow using a slug tracking approach. International Journal of Heat and Mass Transfer, 165, 120664.
https://doi.org/10.1016/j.ijheatmasstransfer.2020.120664
Santana, A. L. B., Marcelino Neto, M. A., & Morales, R. E. M. (2020). Pressure Drop of Horizontal Air–Water Slug Flow in Different Configurations of Corrugated Pipes. Journal of Fluids Engineering, 142(11).
https://doi.org/10.1115/1.4047676
Rodrigues, R. L. P., Cozin, C., Naidek, B. P., Marcelino Neto, M. A., da Silva, M. J., & Morales, R. E. M. (2020). Statistical features of the flow evolution in horizontal liquid-gas slug flow. Experimental Thermal and Fluid Science, 119, 110203.
https://doi.org/10.1016/j.expthermflusci.2020.110203
Rosas, L. M. M., Bassani, C. L., Alves, R. F., Schneider, F. A., Marcelino Neto, M. A., Morales, R. E. M., & Sum, A. K. (2018). Measurements of horizontal three‐phase solid‐liquid‐gas slug flow: Influence of hydrate‐like particles on hydrodynamics. AIChE Journal, 64(7), 2864–2880.
https://doi.org/10.1002/aic.16148
Rosa, E. S., Mazza, R. A., Morales, R. E., Rodrigues, H. T., & Cozin, C. (2015). Analysis of slug tracking model for gas–liquid flows in a pipe. Journal of the Brazilian Society of Mechanical Sciences and Engineering, 37(6), 1665–1686.
https://doi.org/10.1007/s40430-015-0331-7
Ofuchi, C. Y., Eidt, H. K., Rodrigues, C. C., Dos Santos, E. N., Dos Santos, P. H. D., Da Silva, M. J., Neves, F., Jr., Domingos, P. V. S. R., & Morales, R. E. M. (2019). Multiple Wire-Mesh Sensors Applied to the Characterization of Two-Phase Flow inside a Cyclonic Flow Distribution System. Sensors, 19(1), 193.
https://doi.org/10.3390/s19010193
Lino, L. H. M., Eidt, H. K., Rodrigues, C. C., Ofuchi, C. Y., Santos, P. H. D., Neves, F., Jr., Silva, M. J., & Morales, R. E. M. (2019, July 28). Experimental Analysis of a Liquid-Gas Two-Phase Flow in a Flow Distributor. Volume 4: Fluid Measurement and Instrumentation; Micro and Nano Fluid Dynamics. ASME-JSME-KSME 2019 8th Joint Fluids Engineering Conference.
https://doi.org/10.1115/ajkfluids2019-5443
Rodrigues, C. C., Eidt, H. K., Dunaiski, R., Ofuchi, C. Y., Neves, F., Jr., Santos, P. H. D., & Morales, R. E. M. (2017, July 30). Numerical Study of Transient Flow and the Influence of Height and Viscosity in a Cyclonic Chamber in a Distribution System. Volume 1B, Symposia: Fluid Measurement and Instrumentation; Fluid Dynamics of Wind Energy; Renewable and Sustainable Energy Conversion; Energy and Process Engineering; Microfluidics and Nanofluidics; Development and Applications in Computational Fluid Dynamics; DNS/LES and Hybrid RANS/LES Methods. ASME 2017 Fluids Engineering Division Summer Meeting.
https://doi.org/10.1115/fedsm2017-69311
Laboratory Facilities
NUEM is one of the Brazil largest multiphase test facilities. We provide world leading expertise within multiphase technology and a wide range of excellent experimental facilities for R&D applications.
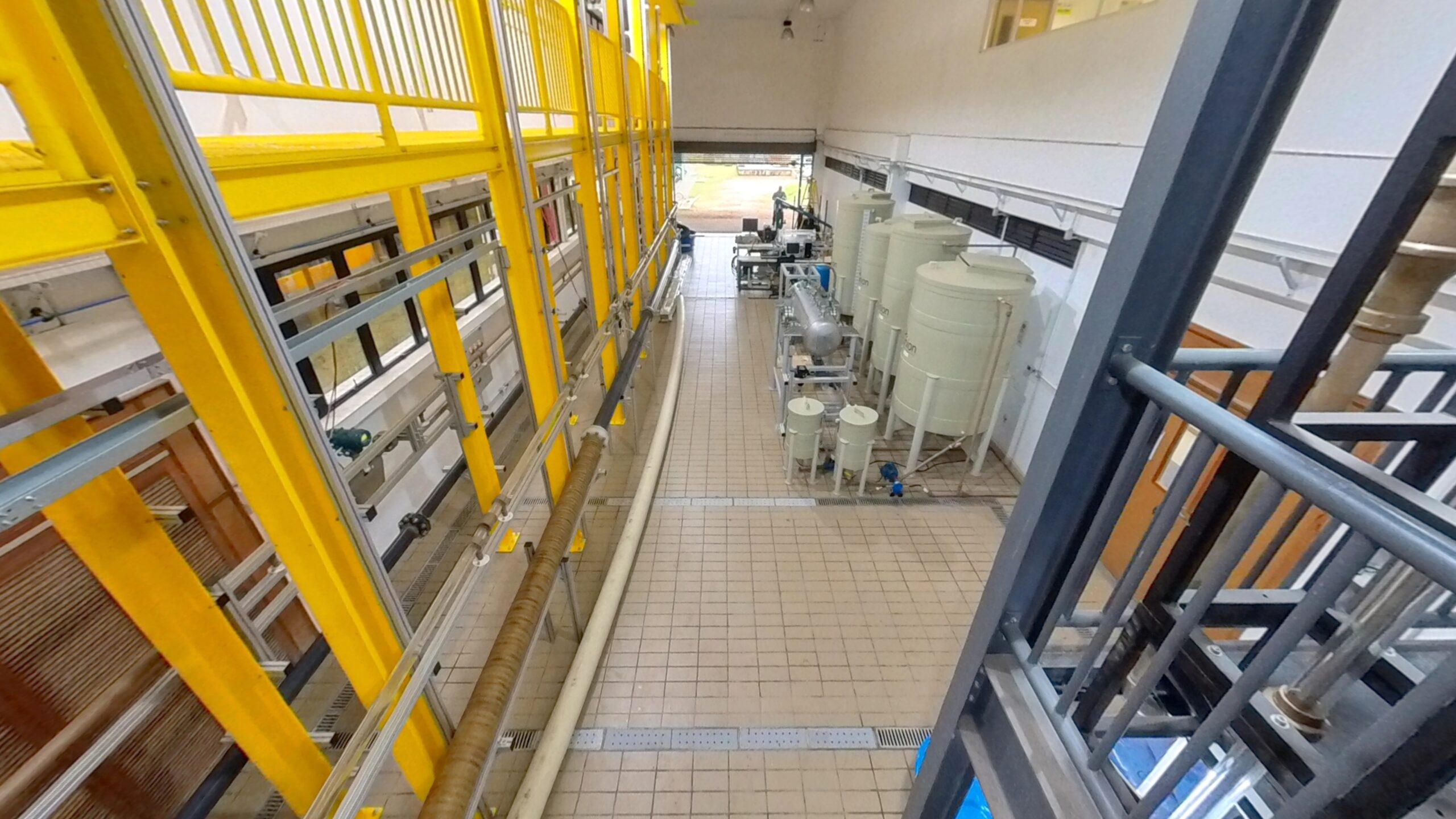
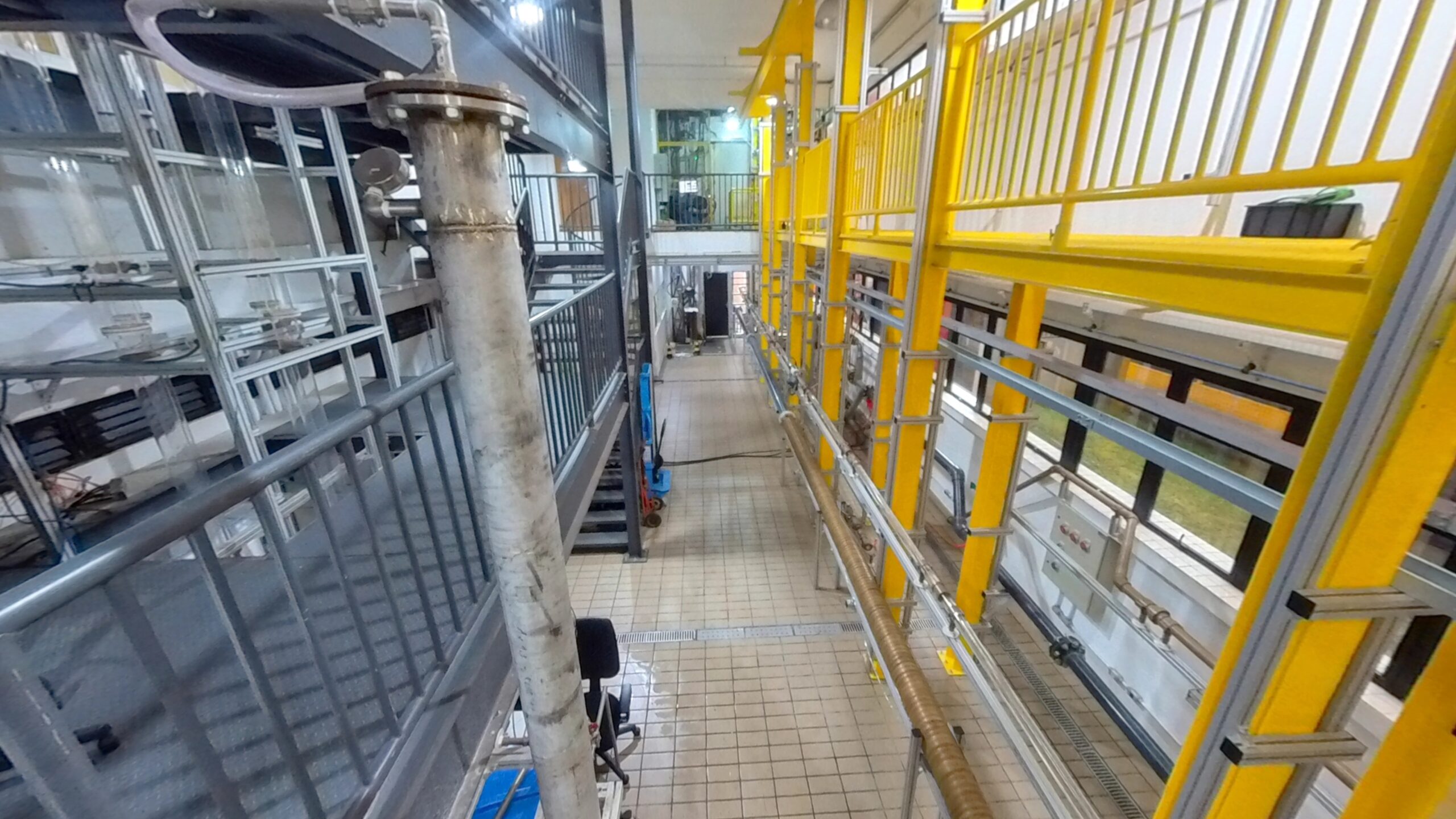
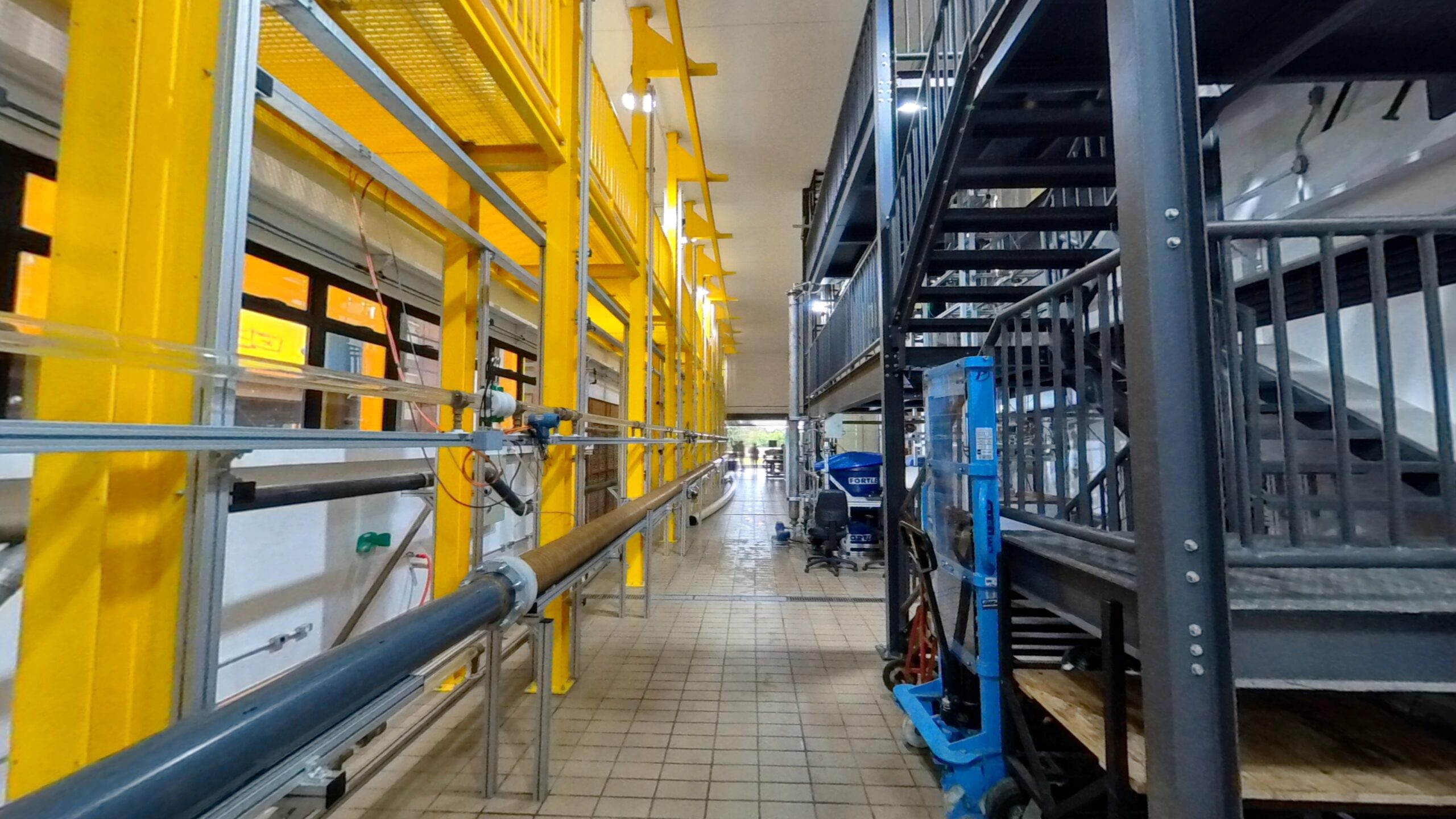
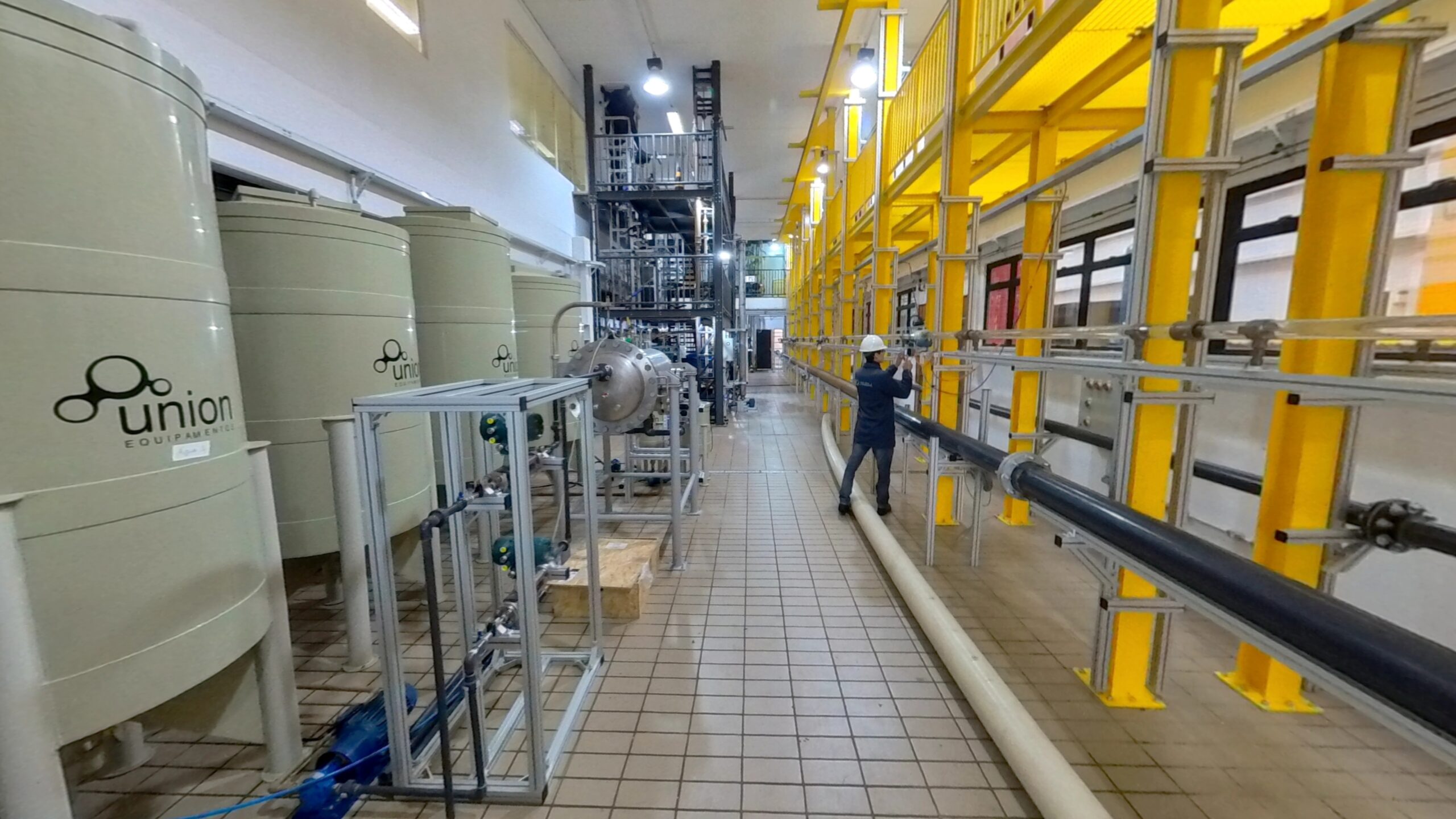
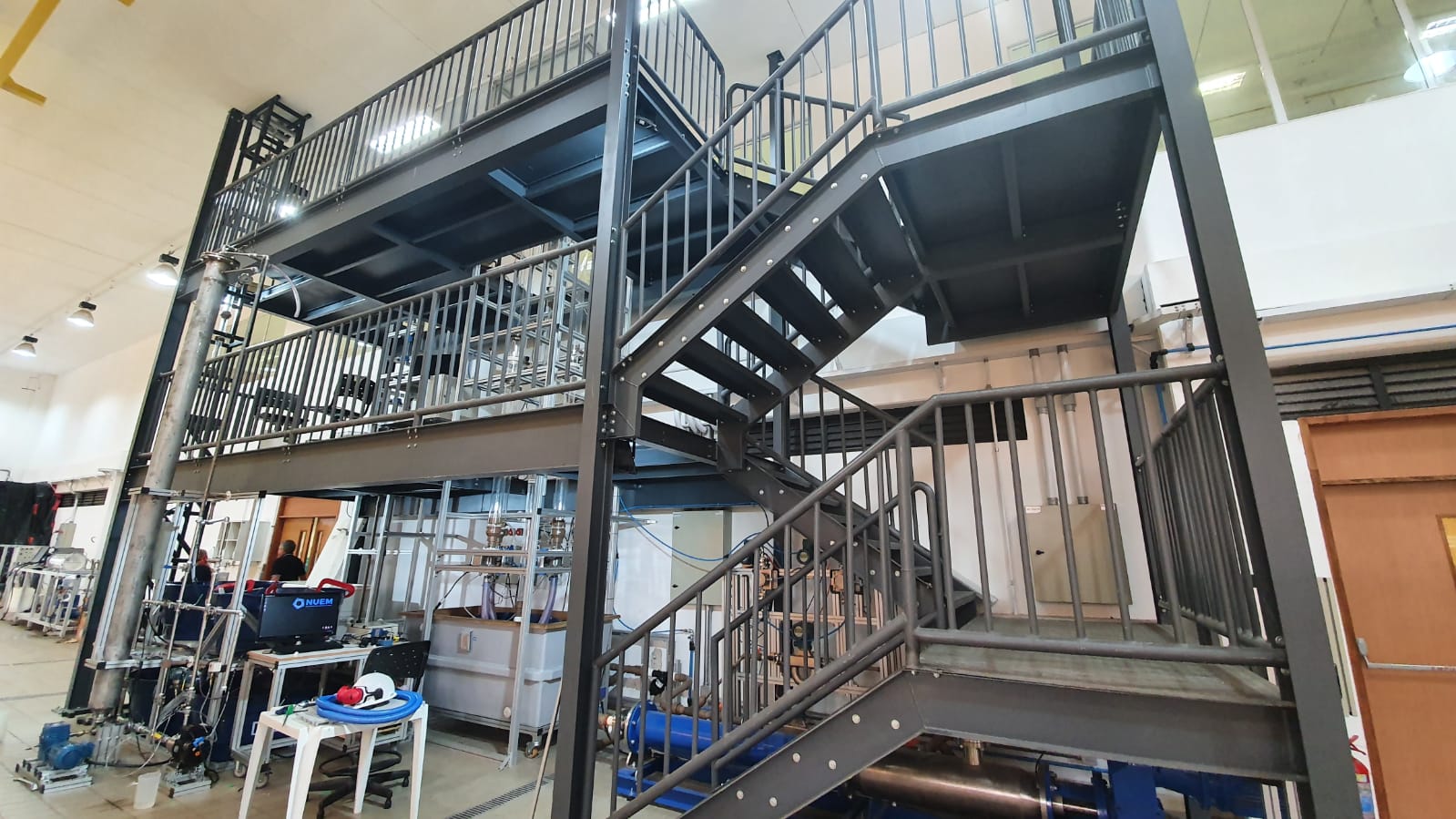
